New electrolyzer tech key for clean hydrogen growth
Advances in electrolyzer technology will help create a clean hydrogen industry that can produce at scale and competitively from a largely intermittent power source.
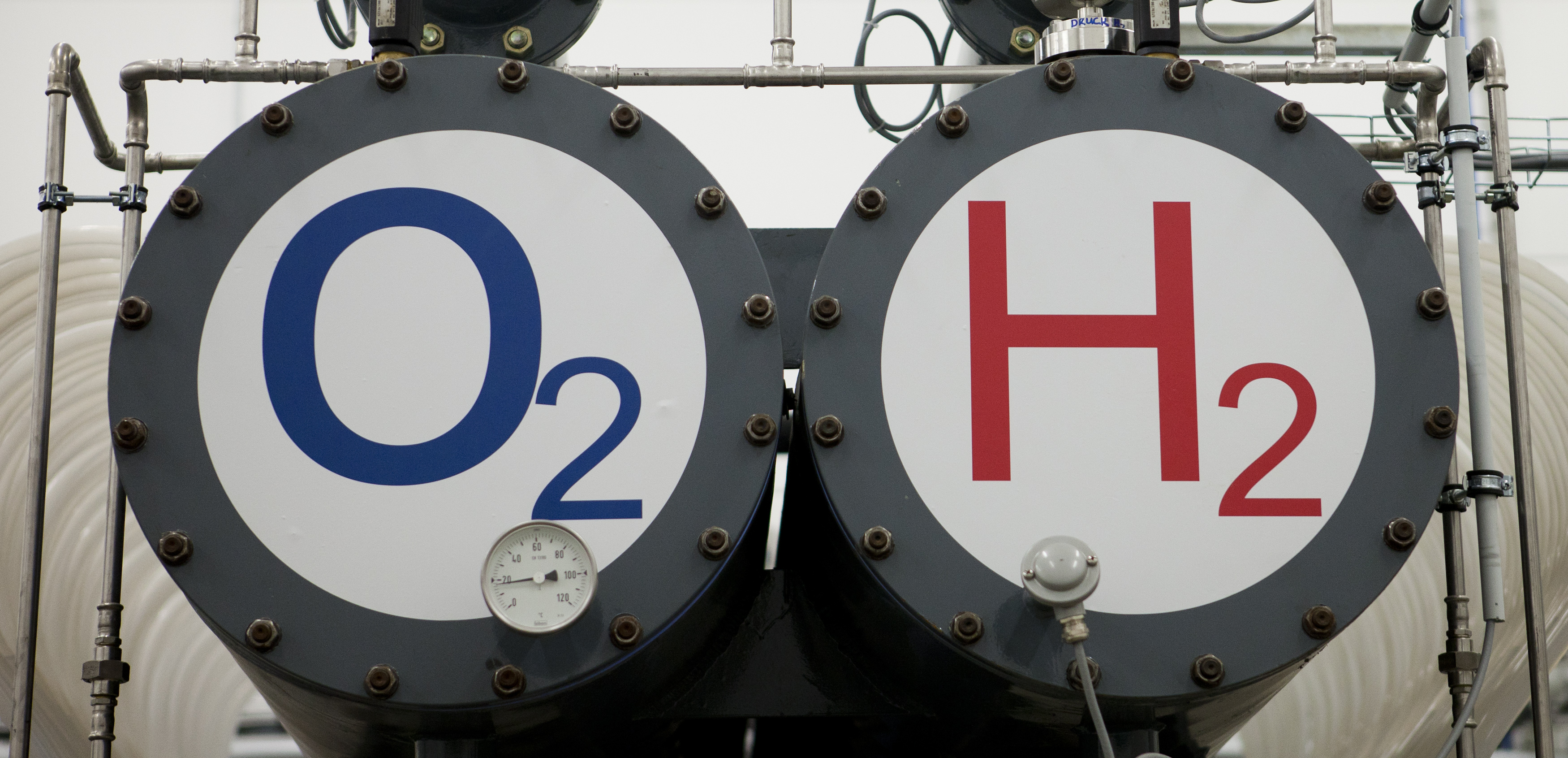
Related Articles
Clean hydrogen can be produced by using emission-free electricity to split water molecules in a process called electrolysis, and companies big and small are racing to find the technology that is most efficient, economical, and scalable.
Electrolysis is achieved using an electrolyzer, of which there are several different types that are at, or close to, commercialization, including alkaline, proton exchange membrane (PEM), solid oxide, and anion exchange membrane (AEM).
Each of the electrolyzer technologies have their advantages and disadvantages, with alkaline and PEM the most commercially mature, but so far none of those on offer have solved the problem of mass-produced clean hydrogen at an acceptable cost.
“There are lots of startups that are trying to fix the problems of alkaline and PEM electrolyzers. But I think the critical question here, just like in most other cases, is whether small scale projects will ever become large scale projects,” says Aliaksei Patonia, Research Fellow at The Oxford institute for Energy Studies (OIES).
“There's a high risk of their failure as it often takes years for a something like this to become a massively used product.”
Electrolyzers’ performance features represent trade-offs among multiple factors such as cost, quantity of noble metals used, technological readiness, and the ability to operate in a flexible mode, Patonia wrote in a jointly-authored research paper with Senior Research Fellow at OIES Rahmatallah Poudineh.
Research into addressing these trade-offs has moved into warp speed in recent years as the shift toward mass production of clean hydrogen becomes increasingly necessary to decarbonize hard-to-abate sectors.
Nameplate Electrolyzer Annual Capacity by Technology (GW)
(Click to enlarge)
Source: Clean Energy Associates (CEA) database from 'Green Hydrogen Supply, Technology, and Policy Report'.
Old tech, new power source
Alkaline electrolyzers have been mass producing hydrogen for more than a hundred years and offer numerous advantages, according to Patonia’s and Poudineh’s OIES study ‘Cost-competitive green hydrogen: how to lower the cost of electrolysers?’
The technology is the most cost competitive, employs low-cost components for both electrodes and porous transport layer materials, and uses cheap, non-noble metals as catalysts.
Their high durability and tolerance to impurities grants them relatively long life-cycles and low maintenance costs, while they also allow for the highest scale-up of hydrogen production at the lowest investment costs, the OIES study notes.
“While still appearing to be undisputable leaders in terms of popularity and scale, alkaline electrolysers have a number of disadvantages, which could significantly limit their use for power-to-hydrogen applications,” according to the OIES.
Due to slow dynamic response times, alkaline electrolyzers run best on uninterrupted and steady electricity sources and, as such, are often found in mountainous areas close hydropower generation sources, or in industrial settings where they are fed from the grid.
However, hydroelectric resources are limited in size and geographic availability, and constant emission-free baseload electricity is unavailable without the use of buffering solutions such as batteries, which remain expensive and relatively undeveloped.
When running on fluctuating power sources, including renewables like wind and solar, alkaline electrolyzers are considerably less efficient.
Also, since the materials and components within the electrolyzers are optimized for steady power inputs, variable power sources can lead to accelerated degradation and increase the need for more frequent maintenance and replacements.
The electrolyzers also operate at lower pressure than alternative technologies, which adds extra steps in the production process as the final product must be compressed for storage and transportation.
Recent technological developments have helped to improve the alkaline electrolyzer efficiencies, including the introduction of pressurization and novel catalysts, but potential improvements are limited.
Flexble but expensive
Proton exchange membrane (PEM) electrolyzers are also a relatively mature technology developed in the 1960s to overcome the disadvantages of alakaline electrolyzers and, as the technology develops, are the most promising to work alongside variable renewable power sources.
PEM eletcrolysers are highly efficient with a current density of up to 3-5 times that of alkaline electrolyzers, according to the Clean Energy Association (CEA).
They are also able to ramp up and ramp down without any major loss of production levels.
“PEM electrolysis provides a sustainable solution for the production of hydrogen, and is well suited to couple with energy sources such as wind and solar,” according to the study ‘A Comprehensive review on PEM water electrolysis’ published in the International Journal of Hydrogen Energy.
“However, due to low demand in electrolytic hydrogen in the last century, little research has been done on PEM electrolysis with many challenges still unexplored.”
One such challenge is that the materials used in the electrolyzer reside within the platinum group of metals and are exceedingly rare, with just around 10 tons of iridium extracted every year from mines in South Africa and Russia.
Their rarity makes essential metals expensive, a serious problem when scaling up production.
Current production of iridium and platinum for PEM electrolyzers will only support an estimated 3 GW-7.5 GW annual manufacturing capacity, compared to an estimated annual manufacturing requirement of around 100 GW by 2030, according to the International Renewable Energy Agency (IRENA).
As the hydrogen industry grows, research into finding a suitable substitute for iridium within PEM electrolyzers has become key, says Jeff Erhardt, CEO and Director of clean chemistry company Mattiq.
Mattiq says it has conducted one of the world’s most comprehensive studies into identifying alternative materials to iridium for PEM electrolyzers.
Using techniques analogous to the high throughput experimentation that transformed the world of drug development and was accelerated by artificial intelligence, the company is exploring alternative catalysts that are mixtures of metals that retain the performance of iridium-based catalysts.
“We used the development platform that we created, starting from the nano material level, to explore millions upon millions of unique combinations of materials to understand how they behave in a chemical reaction, how to scale them up and then integrate them into electrolyzer devices,” says Erhardt.
The process is comparable to the COVID vaccine development, he says, where massive parallel experimentation on large data sets helped find the right molecular combination for an effective vaccine within months rather than years.
Mattiq, with just a couple of dozen employees, has explored close to 10 million different novel materials as potential alternatives to pure iridium and, from that, has identified around 500 set of families that show promise.
“We now have identified materials that go all the way from the nano level through the scale up and we're in the middle of that industrial validation right now that have around 80% reduction in the amount of iridium in them and perform at least as well as the standard benchmarks,” Erhardt says.
Success in this area would put PEM electrolyzers steps ahead in the race to find the right technology for an expanding industry.
By Paul Day